Extending the lifespan of
motor bearings and preventing premature failure is essential for maintaining the efficiency and reliability of electric motors. Here are some tips to help you achieve this:
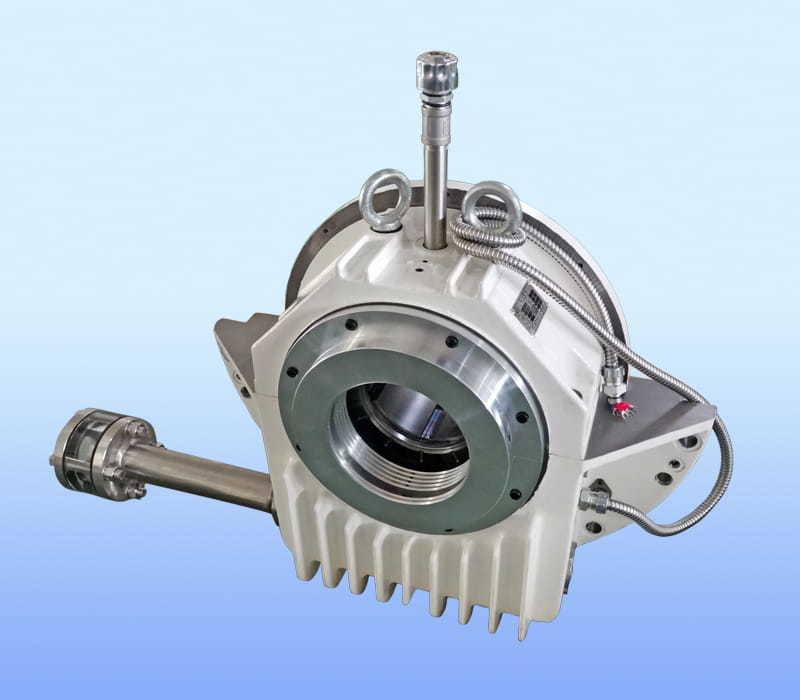
Proper lubrication: Regularly lubricate the motor bearings with the manufacturer-recommended lubricant. Use the correct amount and ensure the lubricant is clean and free from contaminants. Lubrication reduces friction and wear, extending bearing life.
Keep it clean: Keep the motor environment clean to prevent dirt, dust, and other debris from entering the motor and contaminating the bearings. Consider using seals and shields to protect the bearings from external contaminants.
Correct installation: Ensure proper installation of the bearings. Misalignment or incorrect assembly can lead to premature failure. Follow the manufacturer's guidelines and use the appropriate tools and techniques for installation.
Balancing and alignment: Ensure the motor and driven equipment are correctly aligned and balanced. Misalignment can cause excessive stress on the bearings, leading to early failure.
Temperature monitoring: Regularly monitor the operating temperature of the motor bearings. High temperatures can indicate overloading, lack of lubrication, or other issues that need attention.
Vibration analysis: Implement a vibration monitoring program to detect early signs of bearing wear. Unusual vibrations may indicate misalignment or imbalances, and timely detection can prevent further damage.
Load management: Avoid overloading the motor beyond its rated capacity. Excessive loads put extra stress on the bearings and can lead to premature failure.
Frequent inspections: Regularly inspect the motor bearings for signs of wear, damage, or corrosion. Early detection of issues allows for timely maintenance or replacement.
Temperature and moisture control: Maintain a stable operating environment for the motor, avoiding extreme temperatures and moisture, which can promote corrosion and accelerate wear.
Avoid excessive starts and stops: Frequent starts and stops can cause additional stress on the bearings. Consider implementing soft-start and soft-stop controls to reduce wear during motor acceleration and deceleration.
Proper handling: When replacing bearings, ensure proper handling procedures to avoid damage during transportation and installation.
Training and maintenance practices: Ensure that maintenance personnel are adequately trained in motor maintenance practices, including proper handling, lubrication, and troubleshooting.
Implement preventive maintenance: Develop a comprehensive preventive maintenance program that includes regular inspections, lubrication schedules, and proactive measures to detect and address potential issues before they become critical.
By following these guidelines and maintaining a proactive approach to motor bearing maintenance, you can significantly extend the lifespan of the bearings and prevent premature failures, saving on repair costs and downtime.